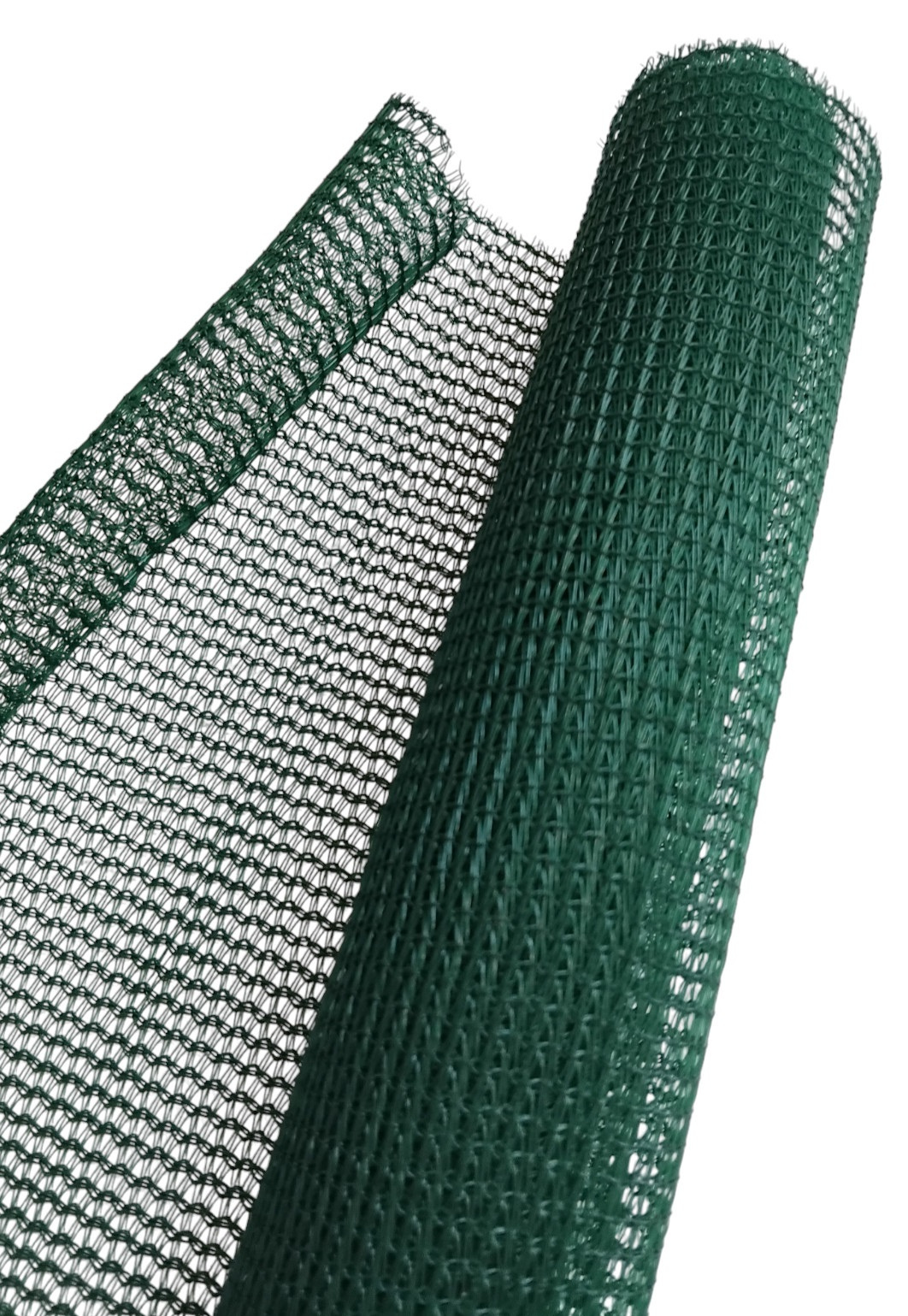
Infuzja próżniowa to zaawansowana technologia produkcji kompozytów, która jest szeroko stosowana w przemyśle laminatów i materiałów kompozytowych. Ten proces polega na wprowadzeniu żywicy do formy laminatu za pomocą próżni, co umożliwia dokładne nasycenie materiału i wyeliminowanie pęcherzyków powietrza. Jednym z kluczowych elementów w tym procesie jest siatka do infuzji próżniowej, która odgrywa istotną rolę w równomiernym rozprowadzaniu żywicy po całej powierzchni laminatu.
Czym jest siatka do infuzji próżniowej?
Siatka do infuzji próżniowej (ang. vacuum infusion mesh) to materiał o otwartej strukturze, najczęściej wykonany z polimerów, takich jak polietylen. Jej głównym zadaniem jest zapewnienie optymalnego przepływu żywicy przez laminat, co jest kluczowe dla uzyskania wysokiej jakości kompozytu.
Działa ona w ten sposób, że umożliwia równomierne rozprowadzanie żywicy pod próżnią na całej powierzchni w bardzo kontrolowany sposób. Dzięki niej unika się zatorów i miejsc, w których mogłoby dojść do nierównomiernego nasączenia materiału, co mogłoby wpłynąć na jego wytrzymałość i trwałość.
Jak działa infuzja próżniowa?
Proces infuzji próżniowej składa się z kilku kroków:
-
Przygotowanie formy: Najpierw w formie układa się suchy materiał wzmacniający, np. tkaninę z włókna szklanego, węglowego lub aramidowego.
-
Rozłożenie siatki do infuzji: Siatka umieszczana jest na powierzchni materiału wzmacniającego, a następnie przykrywana specjalną folią próżniową.
-
Podłączenie systemu próżniowego: Po zamknięciu formy żywica jest wciągana do niej przez otwory za pomocą pompy próżniowej. Żywica przepływa przez siatkę, która zapewnia jej równomierny rozkład.
-
Nasycenie materiału: Żywica wypełnia wszystkie przestrzenie między włóknami materiału, a siatka pomaga w uniknięciu tzw. suchych miejsc (ang. dry spots), które mogłyby osłabić kompozyt.
-
Utwardzanie: Po zakończeniu infuzji próżniowej następuje proces utwardzania, który może odbywać się w temperaturze pokojowej lub w piecu, w zależności od wymagań materiału i rodzaju użytej żywicy.
Zalety stosowania siatki do infuzji próżniowej
Siatka do infuzji próżniowej ma kilka istotnych zalet, które sprawiają, że jest to niezastąpiony element w produkcji kompozytów:
-
Równomierne rozprowadzenie żywicy: Siatka zapewnia, że żywica jest wciągana w kontrolowany sposób i równomiernie nasyca cały materiał kompozytowy, co eliminuje ryzyko powstawania suchych miejsc.
-
Zmniejszenie wagi kompozytu: Proces infuzji próżniowej pozwala na użycie dokładnie takiej ilości żywicy, jaka jest potrzebna. Dzięki temu możliwe jest ograniczenie nadmiaru materiału, co prowadzi do obniżenia wagi finalnego produktu.
-
Wysoka jakość kompozytu: Siatka do infuzji pozwala na uzyskanie kompozytów o bardzo wysokiej jakości, bez pęcherzyków powietrza, z idealnie nasyconymi włóknami. To przekłada się na wytrzymałość mechaniczną i trwałość produktów.
-
Oszczędność materiału: Dzięki kontroli przepływu żywicy można zminimalizować straty materiału, co jest istotne w produkcji na większą skalę.
Zastosowanie siatki do infuzji próżniowej
Siatka do infuzji próżniowej jest szeroko stosowana w różnych sektorach przemysłu kompozytowego, m.in.:
- Przemysł lotniczy i kosmiczny: Produkcja lekkich, wytrzymałych elementów strukturalnych.
- Przemysł motoryzacyjny: Tworzenie karoserii i innych komponentów z włókien węglowych.
- Przemysł jachtowy: Produkcja kadłubów i innych części łodzi, gdzie kluczowa jest niska waga i odporność na korozję.
- Przemysł energetyki wiatrowej: Produkcja łopat turbin wiatrowych o dużej wytrzymałości.
Podsumowanie
Siatka do infuzji próżniowej to niezwykle ważny element w procesie produkcji laminatów i kompozytów. Jej właściwe zastosowanie zapewnia równomierne nasycenie materiału żywicą, co przekłada się na wysoką jakość i trwałość finalnych produktów. Dzięki swojej funkcji, siatka pomaga w optymalizacji procesu infuzji, co ma bezpośredni wpływ na efektywność produkcji i właściwości użytkowe wyrobów kompozytowych.
W przyszłości można spodziewać się dalszego rozwoju tej technologii, co pozwoli na jeszcze większą precyzję w kontroli procesu i optymalizację materiałów stosowanych w zaawansowanych zastosowaniach przemysłowych.