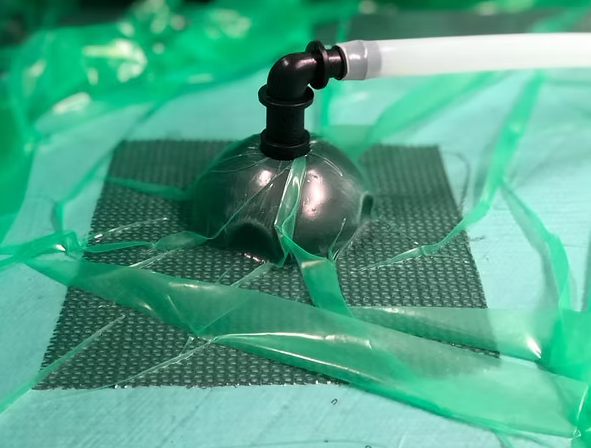
Infuzja próżniowa (ang. vacuum infusion) to zaawansowana metoda produkcji kompozytów, która zyskuje coraz większe znaczenie w różnych gałęziach przemysłu, takich jak lotnictwo, motoryzacja, przemysł morski, budownictwo czy energia wiatrowa. Technika ta polega na zastosowaniu próżni do wciągania żywicy do materiału wzmacniającego, jak włókno szklane, węglowe czy aramidowe, co pozwala na stworzenie wytrzymałych i lekkich elementów konstrukcyjnych o wysokiej jakości.
Na czym polega proces infuzji próżniowej?
Proces infuzji próżniowej jest stosunkowo prosty, choć wymaga precyzyjnego planowania i przygotowania materiałów. Obejmuje on kilka kluczowych kroków:
Przygotowanie formy: Na początku forma, w której zostanie wytworzony kompozyt, jest dokładnie przygotowywana. Może być ona wykonana z materiałów takich jak aluminium, stal czy kompozyty poliestrowe.
Ułożenie włókien: Do formy umieszczane są suche warstwy włókien (np. szklanych, węglowych), które będą wzmacniały ostateczny produkt.
Zastosowanie membrany i wytworzenie próżni: Po ułożeniu materiałów wzmacniających cała forma jest szczelnie pokrywana specjalną folią, a system rur i zaworów tworzy wewnątrz próżnię. Dzięki temu powietrze jest usuwane z formy.
Wprowadzenie żywicy: Pod wpływem próżni żywica jest równomiernie wciągana do formy, wypełniając pory między włóknami. Dzięki tej technice unika się powstawania pęcherzyków powietrza, co zwiększa wytrzymałość i jakość końcowego produktu.
Utwardzanie: Po rozprowadzeniu żywicy, cały układ jest pozostawiony do utwardzenia, co może wymagać podgrzewania lub odczekania kilku godzin w zależności od użytego materiału.
Dlaczego infuzja próżniowa jest ważna w przemyśle?
Infuzja próżniowa niesie ze sobą wiele korzyści, które sprawiają, że jest to jedna z najbardziej preferowanych metod produkcji kompozytów w nowoczesnym przemyśle. Oto kilka kluczowych powodów:
Wyższa jakość produktu: Dzięki precyzyjnej kontroli nad ilością użytej żywicy oraz eliminacji pęcherzyków powietrza, infuzja próżniowa pozwala na uzyskanie kompozytów o znacznie lepszych właściwościach mechanicznych. Produkty te są bardziej wytrzymałe, lżejsze i odporne na czynniki zewnętrzne.
Oszczędność materiałów: Tradycyjne metody, jak laminowanie ręczne, mogą prowadzić do nadmiaru żywicy w produkcie. W infuzji próżniowej wykorzystuje się dokładnie tyle żywicy, ile jest potrzebne, co redukuje marnotrawstwo i obniża koszty produkcji.
Lżejsze konstrukcje: Dzięki precyzyjnemu dozowaniu żywicy oraz optymalnemu wykorzystaniu materiałów wzmacniających, elementy wytwarzane tą metodą są lżejsze niż te produkowane tradycyjnie. Jest to kluczowe w przemyśle lotniczym i motoryzacyjnym, gdzie redukcja masy prowadzi do niższego zużycia paliwa i lepszej wydajności.
Ekologia i czystość produkcji: Infuzja próżniowa jest bardziej przyjazna środowisku niż inne techniki, ponieważ pozwala na redukcję emisji lotnych związków organicznych (VOC). Szczelność procesu minimalizuje również ryzyko wycieków czy zanieczyszczeń.
Wszechstronność: Metoda ta może być stosowana do produkcji zarówno małych, jak i dużych komponentów o złożonych kształtach. Z tego powodu znajduje zastosowanie w produkcji elementów kadłubów jachtów, skrzydeł turbin wiatrowych, elementów karoserii samochodów sportowych czy nawet mostów i budynków.
Zastosowania w przemyśle
Wiele branż korzysta z zalet infuzji próżniowej. W przemyśle morskim stosuje się ją do produkcji kadłubów łodzi i jachtów, które muszą być lekkie, ale jednocześnie wytrzymałe na trudne warunki pogodowe. W lotnictwie metoda ta jest używana do produkcji komponentów o niskiej masie i wysokiej wytrzymałości, takich jak skrzydła, kadłuby i elementy podwozia.
W sektorze energii odnawialnej, zwłaszcza przy produkcji turbin wiatrowych, infuzja próżniowa pozwala na tworzenie dużych, lecz jednocześnie lekkich skrzydeł, co przekłada się na wyższą efektywność energetyczną. W motoryzacji technologia ta znajduje zastosowanie w produkcji karoserii i elementów strukturalnych, gdzie ważna jest zarówno estetyka, jak i właściwości mechaniczne.
Podsumowanie
Infuzja próżniowa to technologia o rosnącym znaczeniu w przemyśle kompozytów. Jej liczne zalety, takie jak wyższa jakość, oszczędność materiałów, ekologia oraz wszechstronność, sprawiają, że jest to idealne rozwiązanie w produkcji zaawansowanych, lekkich i wytrzymałych elementów. Rozwój tej technologii z pewnością przyczyni się do dalszej ewolucji wielu gałęzi przemysłu, wspierając innowacje i zrównoważony rozwój.
Na czym polega proces infuzji próżniowej?
Proces infuzji próżniowej jest stosunkowo prosty, choć wymaga precyzyjnego planowania i przygotowania materiałów. Obejmuje on kilka kluczowych kroków:
Przygotowanie formy: Na początku forma, w której zostanie wytworzony kompozyt, jest dokładnie przygotowywana. Może być ona wykonana z materiałów takich jak aluminium, stal czy kompozyty poliestrowe.
Ułożenie włókien: Do formy umieszczane są suche warstwy włókien (np. szklanych, węglowych), które będą wzmacniały ostateczny produkt.
Zastosowanie membrany i wytworzenie próżni: Po ułożeniu materiałów wzmacniających cała forma jest szczelnie pokrywana specjalną folią, a system rur i zaworów tworzy wewnątrz próżnię. Dzięki temu powietrze jest usuwane z formy.
Wprowadzenie żywicy: Pod wpływem próżni żywica jest równomiernie wciągana do formy, wypełniając pory między włóknami. Dzięki tej technice unika się powstawania pęcherzyków powietrza, co zwiększa wytrzymałość i jakość końcowego produktu.
Utwardzanie: Po rozprowadzeniu żywicy, cały układ jest pozostawiony do utwardzenia, co może wymagać podgrzewania lub odczekania kilku godzin w zależności od użytego materiału.
Dlaczego infuzja próżniowa jest ważna w przemyśle?
Infuzja próżniowa niesie ze sobą wiele korzyści, które sprawiają, że jest to jedna z najbardziej preferowanych metod produkcji kompozytów w nowoczesnym przemyśle. Oto kilka kluczowych powodów:
Wyższa jakość produktu: Dzięki precyzyjnej kontroli nad ilością użytej żywicy oraz eliminacji pęcherzyków powietrza, infuzja próżniowa pozwala na uzyskanie kompozytów o znacznie lepszych właściwościach mechanicznych. Produkty te są bardziej wytrzymałe, lżejsze i odporne na czynniki zewnętrzne.
Oszczędność materiałów: Tradycyjne metody, jak laminowanie ręczne, mogą prowadzić do nadmiaru żywicy w produkcie. W infuzji próżniowej wykorzystuje się dokładnie tyle żywicy, ile jest potrzebne, co redukuje marnotrawstwo i obniża koszty produkcji.
Lżejsze konstrukcje: Dzięki precyzyjnemu dozowaniu żywicy oraz optymalnemu wykorzystaniu materiałów wzmacniających, elementy wytwarzane tą metodą są lżejsze niż te produkowane tradycyjnie. Jest to kluczowe w przemyśle lotniczym i motoryzacyjnym, gdzie redukcja masy prowadzi do niższego zużycia paliwa i lepszej wydajności.
Ekologia i czystość produkcji: Infuzja próżniowa jest bardziej przyjazna środowisku niż inne techniki, ponieważ pozwala na redukcję emisji lotnych związków organicznych (VOC). Szczelność procesu minimalizuje również ryzyko wycieków czy zanieczyszczeń.
Wszechstronność: Metoda ta może być stosowana do produkcji zarówno małych, jak i dużych komponentów o złożonych kształtach. Z tego powodu znajduje zastosowanie w produkcji elementów kadłubów jachtów, skrzydeł turbin wiatrowych, elementów karoserii samochodów sportowych czy nawet mostów i budynków.
Zastosowania w przemyśle
Wiele branż korzysta z zalet infuzji próżniowej. W przemyśle morskim stosuje się ją do produkcji kadłubów łodzi i jachtów, które muszą być lekkie, ale jednocześnie wytrzymałe na trudne warunki pogodowe. W lotnictwie metoda ta jest używana do produkcji komponentów o niskiej masie i wysokiej wytrzymałości, takich jak skrzydła, kadłuby i elementy podwozia.
W sektorze energii odnawialnej, zwłaszcza przy produkcji turbin wiatrowych, infuzja próżniowa pozwala na tworzenie dużych, lecz jednocześnie lekkich skrzydeł, co przekłada się na wyższą efektywność energetyczną. W motoryzacji technologia ta znajduje zastosowanie w produkcji karoserii i elementów strukturalnych, gdzie ważna jest zarówno estetyka, jak i właściwości mechaniczne.
Podsumowanie
Infuzja próżniowa to technologia o rosnącym znaczeniu w przemyśle kompozytów. Jej liczne zalety, takie jak wyższa jakość, oszczędność materiałów, ekologia oraz wszechstronność, sprawiają, że jest to idealne rozwiązanie w produkcji zaawansowanych, lekkich i wytrzymałych elementów. Rozwój tej technologii z pewnością przyczyni się do dalszej ewolucji wielu gałęzi przemysłu, wspierając innowacje i zrównoważony rozwój.